Die Verstopfung der Rasterwalzenzellen ist tatsächlich das unvermeidlichste Thema bei der Verwendung von Rasterwalzen. Ihre Erscheinungsformen lassen sich in zwei Fälle unterteilen: die Oberflächenverstopfung der Rasterwalze (Figur.1) und die Verstopfung der Rasterwalzenzellen (Figur. 2).
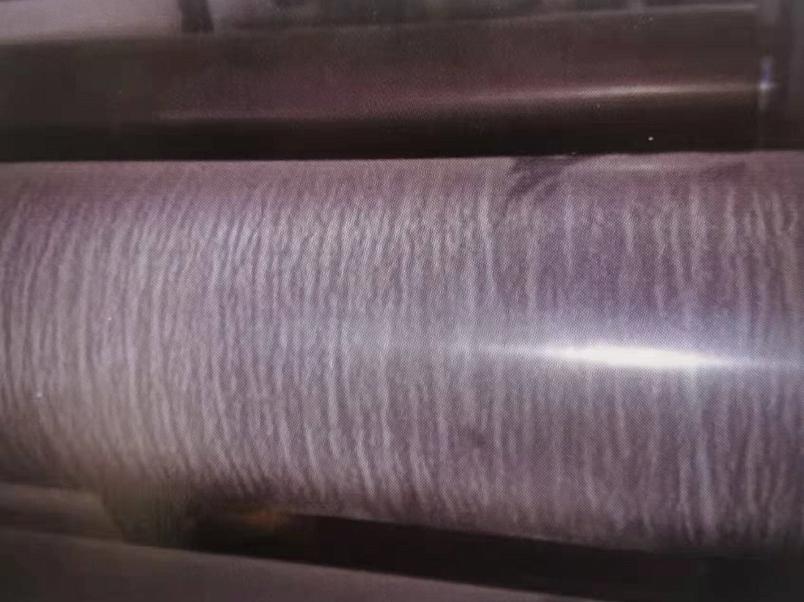
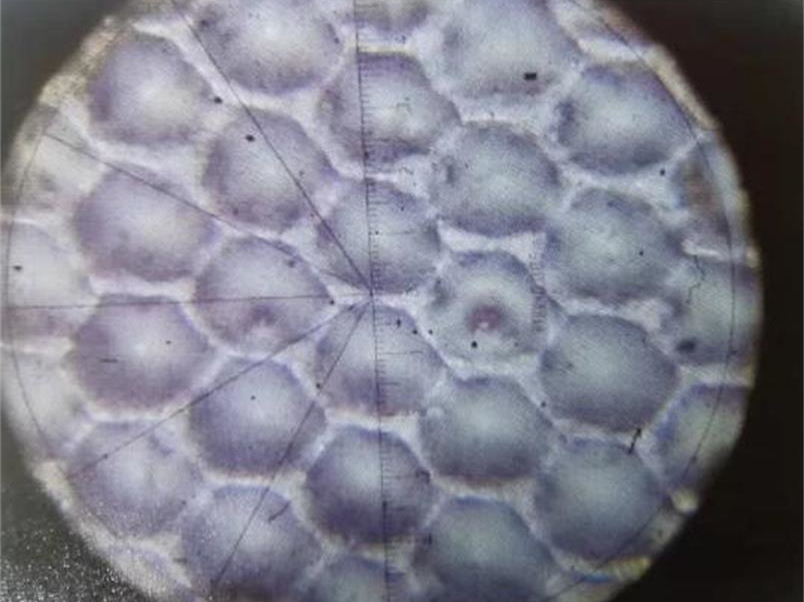
Abbildung .1
Abbildung .2
Ein typisches Flexo-Farbsystem besteht aus einer Farbkammer (geschlossenes Farbzufuhrsystem), einer Rasterwalze, einem Plattenzylinder und einem Substrat. Um qualitativ hochwertige Drucke zu erzielen, ist ein stabiler Farbübertragungsprozess zwischen der Farbkammer, den Rasterwalzenzellen, der Oberfläche der Druckplattenpunkte und der Oberfläche des Substrats erforderlich. Bei diesem Farbübertragungspfad beträgt die Farbübertragungsrate von der Rasterwalze zur Plattenoberfläche etwa 40 %, die Farbübertragung von der Platte zum Substrat etwa 50 %. Es ist ersichtlich, dass eine solche Farbübertragung kein einfacher physikalischer Transfer ist, sondern ein komplexer Prozess, der Farbübertragung, Farbtrocknung und Farbrücklösung umfasst. Mit der immer schneller werdenden Druckgeschwindigkeit der Flexodruckmaschine wird dieser komplexe Prozess nicht nur immer komplizierter, sondern auch die Häufigkeit von Schwankungen bei der Farbübertragung wird immer höher. Auch die Anforderungen an die physikalischen Eigenschaften der Löcher werden immer höher.
Polymere mit Vernetzungsmechanismus werden häufig in Tinten verwendet, wie z. B. Polyurethan, Acrylharz usw., um die Haftung, Abriebfestigkeit, Wasserbeständigkeit und chemische Beständigkeit der Tintenschicht zu verbessern. Da die Tintenübertragungsrate in den Rasterwalzenzellen nur 40 % beträgt, verbleibt der Großteil der Tinte während des gesamten Druckvorgangs am Boden der Zellen. Selbst wenn ein Teil der Tinte ersetzt wird, kann es leicht passieren, dass die Tinte in den Zellen aufgebraucht ist. Die Harzvernetzung erfolgt auf der Oberfläche des Substrats, was zur Verstopfung der Rasterwalzenzellen führt.
Es ist leicht zu verstehen, dass die Oberfläche der Rasterwalze verstopft ist. Im Allgemeinen wird die Rasterwalze unsachgemäß verwendet, sodass die Tinte auf der Oberfläche der Rasterwalze aushärtet und vernetzt, was zu einer Verstopfung führt.
Für Hersteller von Rasterwalzen können Forschung und Entwicklung im Bereich der Keramikbeschichtung, die Verbesserung der Laseranwendungstechnologie und die Verbesserung der Keramikoberflächenbehandlungstechnologie nach der Gravur von Rasterwalzen das Verstopfen der Rasterwalzenzellen verringern. Derzeit werden üblicherweise Methoden verwendet, um die Breite der Maschenwand zu verringern, die Glätte der Mascheninnenwand zu verbessern und die Kompaktheit der Keramikbeschichtung zu verbessern.
Für Druckereien können außerdem die Trocknungsgeschwindigkeit der Tinte, die Auflösung und der Abstand vom Rakelpunkt zum Druckpunkt angepasst werden, um die Verstopfung der Rasterwalzenzellen zu verringern.
Korrosion
Unter Korrosion versteht man das Phänomen punktförmiger Vorsprünge auf der Oberfläche der Rasterwalze, wie in Abbildung 3 dargestellt. Korrosion wird dadurch verursacht, dass das Reinigungsmittel entlang des Keramikspalts in die untere Schicht eindringt, die untere metallische Grundwalze korrodiert und die Keramikschicht von innen aufbricht, wodurch die Rasterwalze beschädigt wird (Abbildung 4, Abbildung 5).
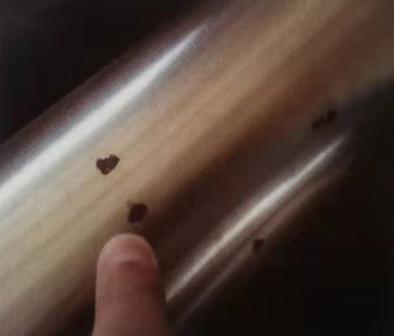
Abbildung 3
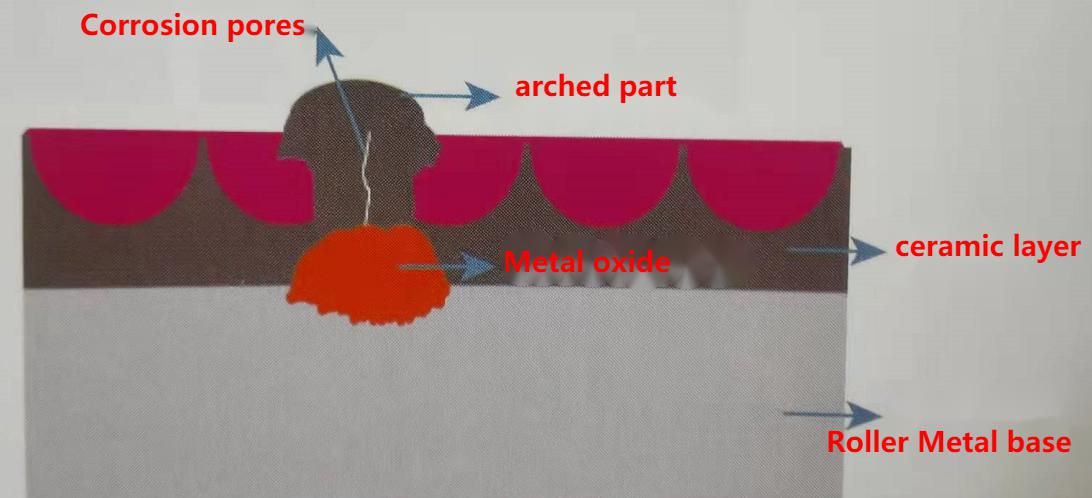
Abbildung 4
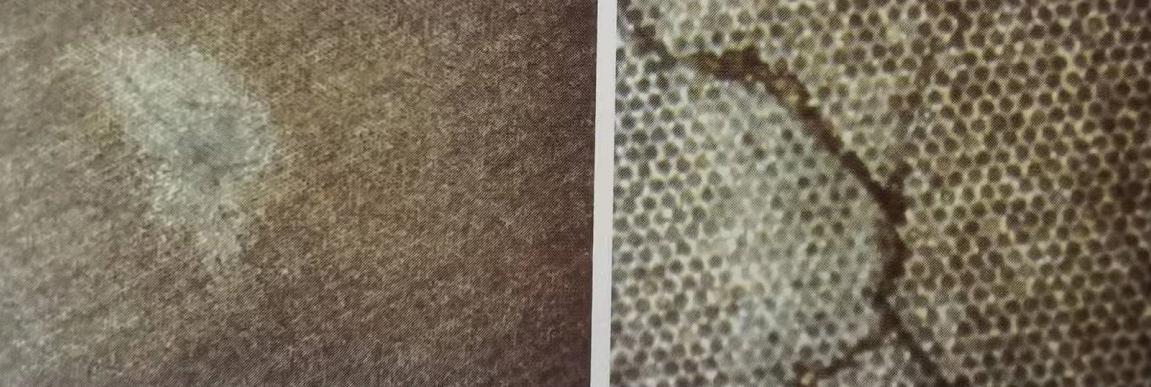
Abbildung 5 Korrosion unter dem Mikroskop
Die Gründe für die Entstehung von Korrosion sind folgende:
① Die Poren der Beschichtung sind groß und die Flüssigkeit kann durch die Poren die Basiswalze erreichen, was zu Korrosion der Basiswalze führt.
② Langfristige Verwendung von Reinigungsmitteln wie starken Säuren und starken Laugen, ohne rechtzeitiges Duschen und Lufttrocknen nach der Verwendung.
3. Die Reinigungsmethode ist falsch, insbesondere bei der Gerätereinigung über einen längeren Zeitraum.
④ Die Lagermethode ist falsch und das Produkt wird über einen längeren Zeitraum in einer feuchten Umgebung gelagert.
⑤ Der pH-Wert der Tinte oder der Zusatzstoffe ist zu hoch, insbesondere bei Tinte auf Wasserbasis.
⑥ Die Rasterwalze wird während des Installations- und Demontagevorgangs beschädigt, was zu einer Änderung des Keramikschichtspalts führt.
Der erste Vorgang wird oft übersehen, da zwischen dem Auftreten von Korrosion und der eventuellen Beschädigung der Rasterwalze viel Zeit vergeht. Wenn Sie das Absackphänomen der Keramik-Rasterwalze feststellen, sollten Sie sich daher rechtzeitig an den Lieferanten der Keramik-Rasterwalze wenden, um die Ursache des Bogens zu untersuchen.
Umlaufende Kratzer
Kratzer auf Rasterwalzen sind die häufigsten Probleme, die die Lebensdauer von Rasterwalzen beeinträchtigen.(Abbildung 6)Dies liegt daran, dass die Partikel zwischen der Rasterwalze und der Rakel unter Druckeinwirkung die Oberflächenkeramik der Rasterwalze aufbrechen und alle Maschenwände in Drucklaufrichtung öffnen, um eine Rille zu bilden. Die Wirkung auf den Druck ist das Auftreten dunklerer Linien.
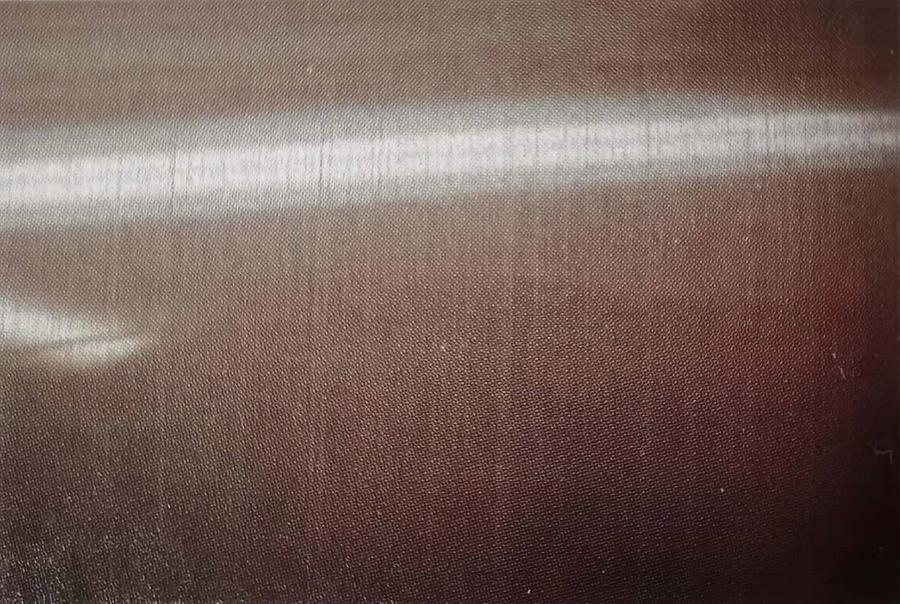
Abbildung 6 Rasterwalze mit Kratzern
Das Hauptproblem von Kratzern ist die Druckänderung zwischen Rakel und Rasterwalze, sodass der ursprüngliche Flächendruck zu einem lokalen Punktdruck wird. Die hohe Druckgeschwindigkeit führt zu einem starken Druckanstieg, der eine erstaunliche Zerstörungskraft aufweist. (Abbildung 7)
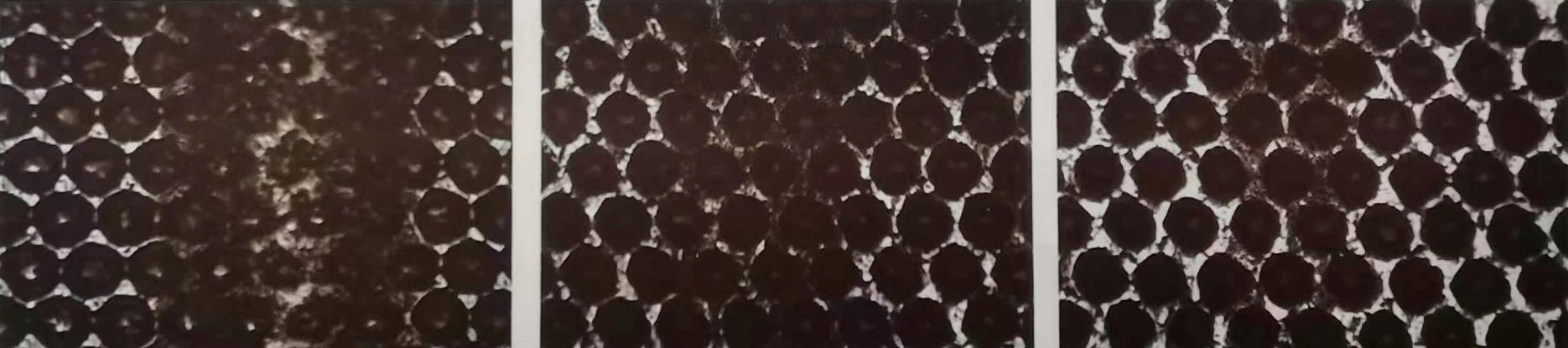
Abbildung 7 starke Kratzer
Allgemeine Kratzer
leichte Kratzer
Je nach Druckgeschwindigkeit bilden sich Kratzer, die den Druck beeinträchtigen, im Allgemeinen innerhalb von 3 bis 10 Minuten. Dieser Druck wird von vielen Faktoren beeinflusst, vor allem von mehreren Aspekten: der Rasterwalze selbst, der Reinigung und Wartung des Rakelsystems, der Qualität, Installation und Verwendung der Rakel sowie Konstruktionsfehlern der Ausrüstung.
1.die Rasterwalze selbst
(1) Die Oberflächenbehandlung der Keramik-Rasterwalze ist nach dem Gravieren nicht ausreichend, und die Oberfläche ist rau und kann leicht den Schaber und die Klinge des Schabers zerkratzen.
Die Kontaktfläche mit der Rasterwalze hat sich verändert, wodurch der Druck erhöht, der Druck vervielfacht und das Netz im Zustand des Hochgeschwindigkeitsbetriebs gebrochen wird.
Auf der Oberfläche der Prägewalze bilden sich Kratzer.
(2) Beim Polieren und Feinschleifen bildet sich eine tiefe Polierlinie. Diese Situation tritt in der Regel bei der Lieferung der Rasterwalze auf, und die leicht polierte Linie beeinträchtigt den Druck nicht. In diesem Fall muss die Druckprüfung an der Maschine durchgeführt werden.
2. die Reinigung und Wartung des Rakelsystems
(1) Unabhängig davon, ob die Höhe der Kammerrakel korrigiert wird, führt eine Kammerrakel mit schlechter Höhe zu ungleichmäßigem Druck. (Abbildung 8)
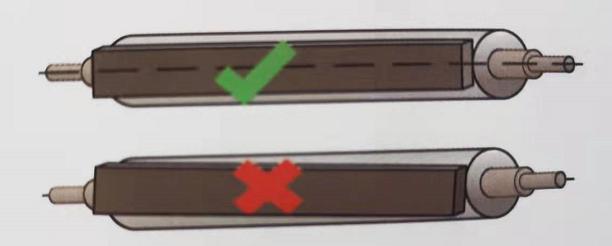
Abbildung 8
(2) Unabhängig davon, ob die Rakelkammer vertikal gehalten wird, vergrößert eine nicht vertikale Farbkammer die Kontaktfläche der Rakel. Dies kann zu einer direkten Beschädigung der Rasterwalze führen. Abbildung 9
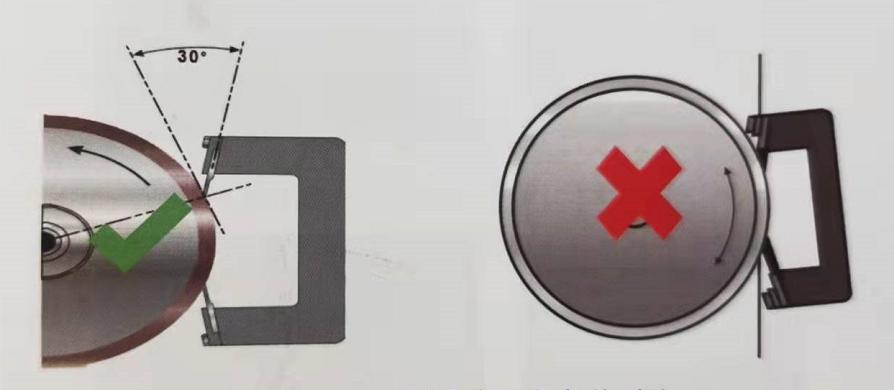
Abbildung 9
(3) Die Reinigung des Kammerrakelsystems ist sehr wichtig. Verhindern Sie, dass Verunreinigungen in das Farbsystem gelangen und sich zwischen Rakel und Rasterwalze festsetzen. Dies kann zu Druckänderungen führen. Trockene Tinte ist ebenfalls sehr gefährlich.
3. Die Installation und Verwendung der Rakel
(1) Installieren Sie die Kammerrakel richtig, um sicherzustellen, dass die Klinge nicht beschädigt ist, die Klinge gerade ohne Wellen ist und perfekt mit dem Klingenhalter kombiniert ist, wie z. B.
Achten Sie darauf, wie in Abbildung 10 gezeigt, dass der Druck auf der Oberfläche der Rasterwalze gleichmäßig bleibt.
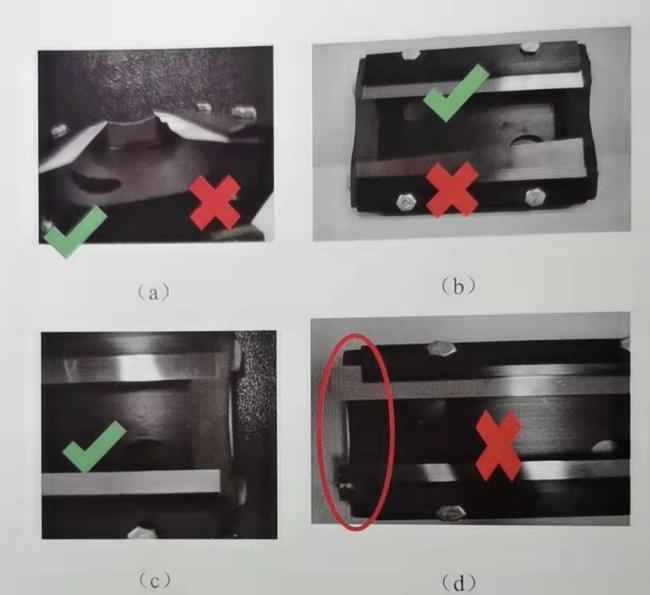
Abbildung 10
(2) Verwenden Sie hochwertige Schaber. Hochwertiger Schaberstahl hat eine dichte Molekülstruktur, wie in Abbildung 11 (a) dargestellt. Nach dem Verschleiß sind die Partikel klein und gleichmäßig. Die Molekülstruktur von minderwertigem Schaberstahl ist nicht dicht genug und die Partikel sind nach dem Verschleiß groß, wie in Abbildung 11 (b) dargestellt.
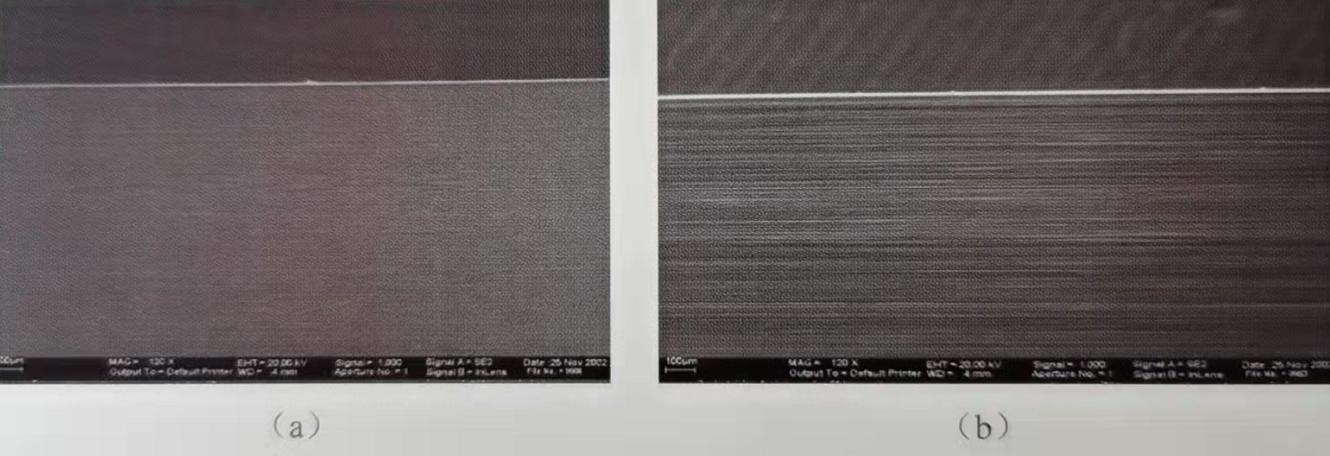
Abbildung 11
(3) Ersetzen Sie das Rakelmesser rechtzeitig. Achten Sie beim Ersetzen darauf, die Messerkante vor Stößen zu schützen. Beim Wechsel auf eine andere Strichzahl der Rasterwalze müssen Sie das Rakelmesser ersetzen. Der Verschleißgrad der Rasterwalze bei unterschiedlichen Strichzahlen ist inkonsistent, wie in Abbildung 12 dargestellt. Das linke Bild zeigt den Zustand der beschädigten Stirnfläche des Rakelmessers bei niedriger Strichzahl. Das rechte Bild zeigt den Zustand der abgenutzten Stirnfläche der Rasterwalze mit hoher Strichzahl zum Rakelmesser. Die Kontaktfläche zwischen Rakelmesser und Rasterwalze mit unterschiedlichem Verschleißgrad verändert sich, was zu Druckänderungen und Kratzern führt.
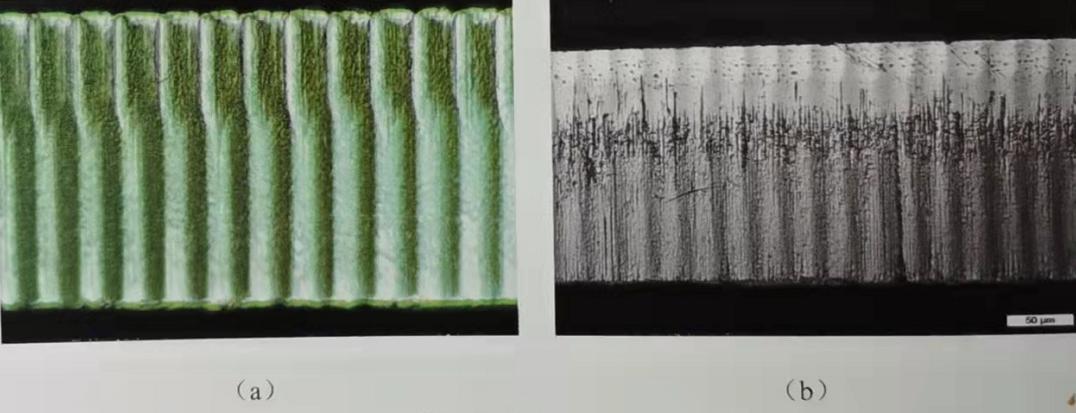
Abbildung 12
(4) Der Druck des Rakels sollte gering sein. Zu hoher Druck verändert die Kontaktfläche und den Winkel zwischen Rakel und Rasterwalze (siehe Abbildung 13). Verunreinigungen können leicht eingedrungen sein, was nach einer Druckänderung zu Kratzern führt. Bei übermäßigem Druck bilden sich am Querschnitt des ausgetauschten Schabers (Abbildung 14) abgenutzte Metallenden. Fällt dieser ab, bleibt er zwischen Schaber und Rasterwalze hängen, was zu Kratzern auf der Rasterwalze führen kann.
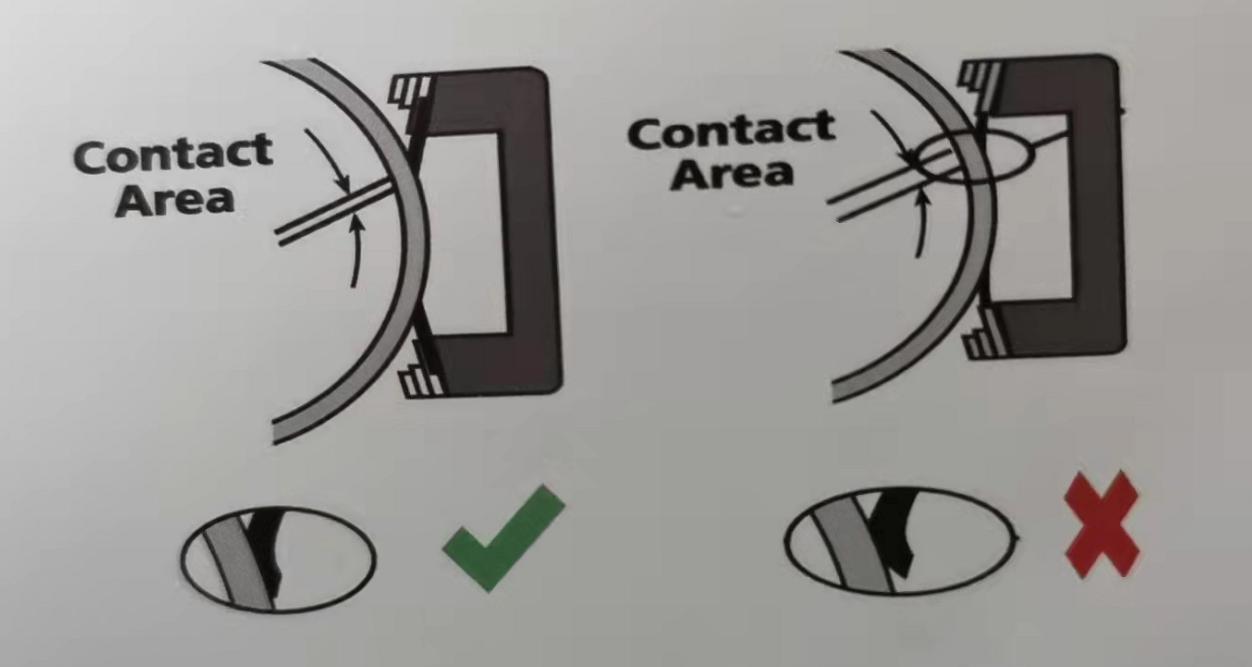
Abbildung 13
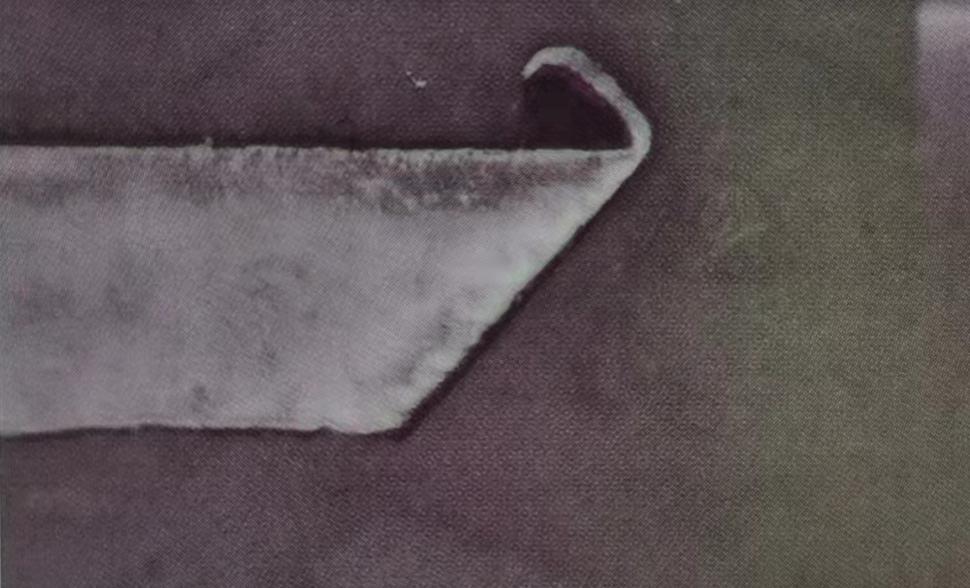
Abbildung 14
4. die Konstruktionsfehler der Ausrüstung
Auch Konstruktionsfehler können leicht zu Kratzern führen, beispielsweise eine Nichtübereinstimmung zwischen dem Design des Farbblocks und dem Durchmesser der Rasterwalze. Eine ungünstige Konstruktion des Rakelwinkels, eine Inkongruenz zwischen Durchmesser und Länge der Rasterwalze usw. führen zu Unsicherheiten. Es ist ersichtlich, dass das Problem von Kratzern in Umfangsrichtung der Rasterwalze sehr komplex ist. Das Beachten von Druckänderungen, rechtzeitige Reinigung und Wartung, die Wahl des richtigen Abstreifers sowie gute und geordnete Arbeitsweisen können das Kratzerproblem erheblich lindern.
Kollision
Obwohl Keramik eine hohe Härte aufweist, handelt es sich um sprödes Material. Unter Einwirkung äußerer Kräfte kann Keramik leicht abfallen und Löcher bilden (Abbildung 15). Beim Be- und Entladen von Rasterwalzen kommt es häufig zu Stößen, oder Metallwerkzeuge fallen von der Walzenoberfläche. Halten Sie die Druckumgebung sauber und vermeiden Sie das Stapeln von Kleinteilen rund um die Druckmaschine, insbesondere in der Nähe des Farbbehälters und der Rasterwalze. Es wird empfohlen, die Rasterwalze sorgfältig zu bearbeiten. Schützen Sie die Walze sorgfältig, um zu verhindern, dass kleine Gegenstände herunterfallen und mit der Rasterwalze kollidieren. Beim Be- und Entladen der Rasterwalze wird empfohlen, diese vor dem Betrieb mit einer flexiblen Schutzhülle zu umwickeln.
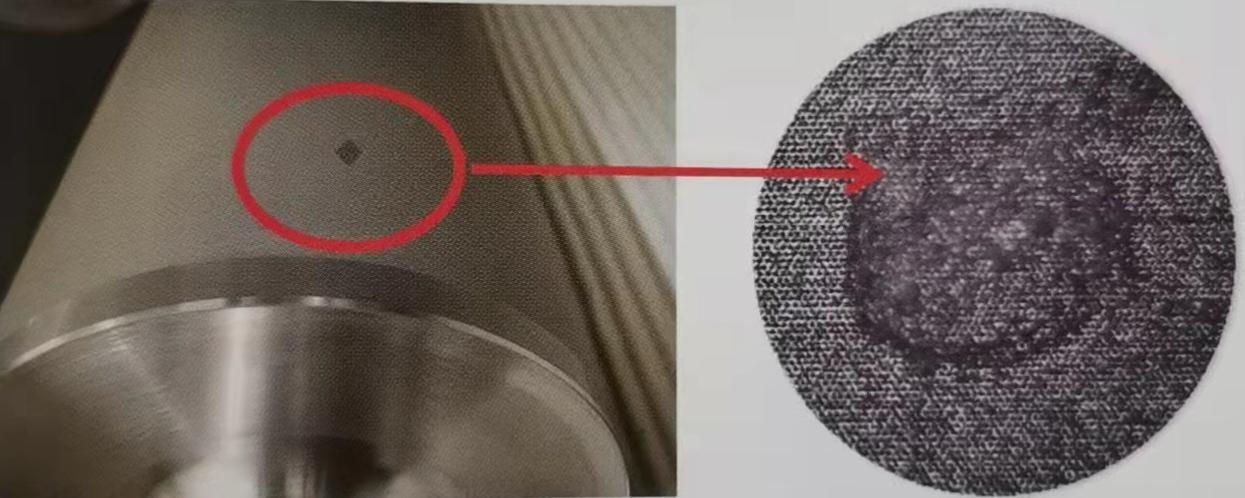
Abbildung 15
Veröffentlichungszeit: 23. Februar 2022